BETWEEN A ROCK AND A HARD PLACE
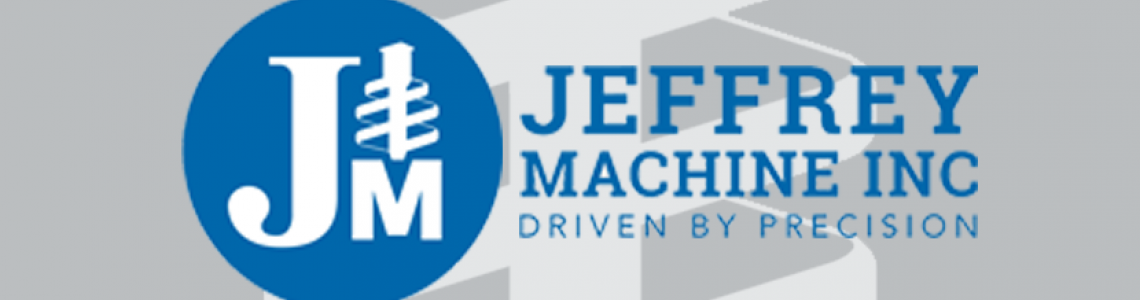
The following article first appeared in Civil Infrastructure and is used here with permission.
What do you do when you’re stuck between a rock and a hard place? In the following case study, a contractor working for the Alabama D.O.T. found himself in exactly this type of situation. This write up explores some of the details of the project and the unique solutions he came up with to complete the job.
Mike Greenwood, owner of Louana Construction in Hueytown, Alabama took an assignment with the D.O.T. to set some lighting poles along I-20 between Birmingham and Atlanta. Two poles needed to be set near the end of one of the entrance ramps. When Mike went out to survey the site for those poles, it gave him an uneasy feeling in the pit of his stomach. According to Mr. Greenwood, this exit is also commonly referred to as ‘death valley’ by locals due to the large number of fatalities that had occurred right at the spot where his jobsite would have to be set up. His men would be working right at the point where cars are accelerating to the speed limit of 65 mph and then attempting to merge into traffic. He had already been warned that the authorities would not allow him to slow traffic at that point. To make matters worse, there was very little space off of the berm. This section of the interstate had been cut out of the rock and there wasn’t much more than 7′ of space between that speeding traffic looking for a place to merge and a 30′ high embankment of solid rock.
Complicating matters even more, the lighting poles had to be set no closer than thirty feet to the road in accordance with federal highway regulations. The thirty foot high embankment was cut at a steep angle. As Mr. Greenwood surveyed the site, he discovered that thirty feet off the road would mean he would have to set the poles a little more than halfway up that steep bank. According to the job specs, the poles had to be set on two and a half foot diameter by eight foot deep concrete foundations. His survey led him to the conclusion that there was no way to get a drilling rig up on the side of that bank. Over the next few days Greenwood explored every option he could think of and nothing seemed to be applicable within the confines of the work area. Drilling and blasting would have most likely brought down the front face of the rock. He even considered ‘dead manning’ a drilling rig by somehow hanging over the side, but that wasn’t feasible either.
He eventually contacted Jeffrey Machine, an auger manufacturer in Birmingham. He always turned to them whenever he ran into a boring problem. If they didn’t have the solution, they would always work with him to devise something that would work. Mike Greenwood spoke with Jeff Sager, one of the company owners, and told him the situation and asked if they had any ideas. Mr. Sager prompted Mike, saying ‘Well, you’ve got a track hoe. Will it reach up there if you had a drilling motor and an auger on it? Do you have the reach to get up there where you’d have to start?”
For those of you that might not know, Sager was referring to a unique evolution in boring technology that has been developing over the years. Several companies have come up with motors that can attach to common construction equipment that can convert them into virtual boring rigs. As an example, the bucket on a backhoe could be taken off, and one of the motors attached to the same bracket that held the bucket. It is powered by the backhoe’s hydraulic system and one of the most attractive benefits is the ability to drill a hole wherever that boom can reach.
Anyway, Mike told him they could get the reach with his Caterpillar 310 track hoe, but that a ‘dangle digger’ wouldn’t have the power to cut a 30′ hole eight feet deep into that rock. Jeff told him about a new digger drive motor being put out by a company named Eskridge that could generate twenty thousand foot pounds of torque. If it worked, that would provide enough power to do the job, but it still wouldn’t dig as fast in that rock as one of his drilling rigs. Mr. Greenwood did some research and talked to several companies that had used the unit in various rock conditions. It seemed like the only feasible solution, so he went ahead and obtained one.
Greenwood didn’t want his crew out in the danger zone a second longer than they had to be so he turned his attention to finding a way to speed up the cutting process of the auger. He made another call to Jeffrey Machine and explained his concerns and asked if they could help him come up with a faster cutter. Mr. Sager recommended that Mike try a smaller diameter tooth. ‘It’s going to give you more pressure per square inch on your tooth and it’s going to cut a lot better. The downside of it is that you’ll go through a lot more teeth’, Sager explained. It made sense, but it hadn’t been done, so Jeffrey Machine provided some teeth for a trial. According to Mr. Greenwood, ‘Jeffrey got us some teeth and we put ’em on another auger on one of our trucks. We went to a spot on the project where there was rock and we drilled an 18″ hole with the normal teeth. We timed ourselves and then moved over about 3′, put these smaller teeth on there and drilled that hole. We went down in about two thirds of the time. The tooth wear was about 70% increase in tooth wear but that’s not a major cost if you can get out of this hazardous location.
Louana Construction fitted the track hoe with the new digger motor and a new auger Jeffrey Machine had tailored to the needs of this specific project. They started the process by taking a jackhammer and cutting out a small level notch in the bank where the drilling was to begin. To get the hole started they started in at an angle and then raised it into a straight up position to drill to the required depth. The edge of the track hoe was way too close to that stream of deadly traffic. It would be lying to say there wasn’t some serious apprehension going on with the Louana crew. What seemed like a total impossibility just a short time before turned into a successful job. By taking advantage of advances in technology and enlisting the aid of helpful and knowledgeable suppliers, the obstacle was overcome. Additionally, they were able to get it done quickly enough to avoid adding to ‘death valley’s’ statistics