3 Must-Know Maintenance Tips for Kelly Bars
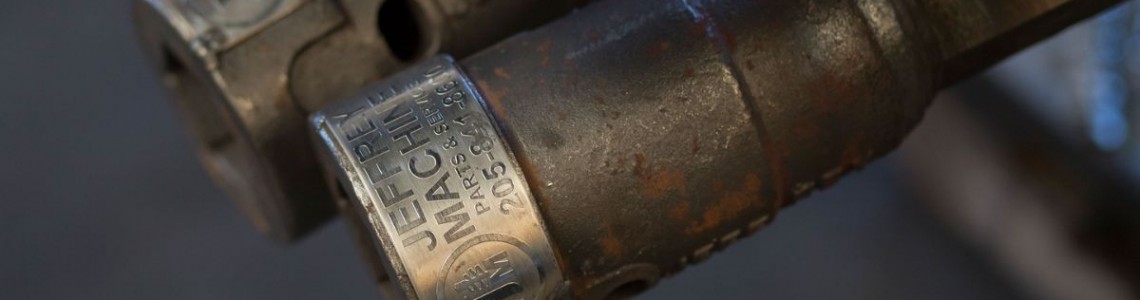
Because Kelly bars are such an integral part of Kelly
drilling rig configurations, it’s important that you treat them with care to
get the most out of your machinery. Kelly configurations are one of the most
utilized drilling methods, and Kelly bars will undergo a lot of stress, wear,
and tear that could potentially comprise their condition and effectiveness.
Here are three must-know maintenance tips for Kelly bars.
Avoid On-Site Repairs
The last thing you want is to grind production to a halt because
you need to perform on-site repairs. The key consideration for avoiding this is
to never run your Kelly bars to their absolute limit. Remember that these bars
are wear items and capable of breaking during the drilling process. While
on-site repairs can be cumbersome and time-consuming on their own, a Kelly bar
that breaks underground will be difficult to extract, creating much longer
delays in your progress.
One of the best maintenance tips is to avoid on-site repairs
whenever possible. Neglecting your Kelly bars will only damage them further and
require more time to fix them, but when they're used in moderation, maintenance
will be substantially smaller and quicker.
Inspect for Damage
Even between scheduled maintenance, you should keep a keen
eye on your Kelly bars to survey for damage or signs of wear. This is as simple
as surveying your Kelly bars for cracks and worn-down areas between uses so
that you can perform preventative maintenance and better preserve your Kelly
bars. You may also find inconsistencies and defections in joints, bolts,
blocks, drive keys, or springs. Furthermore, keep an eye on components like Kelly bar adapters. An
ill-fitting adapter or mount can be very damaging to your Kelly bar.
Grease Moving Parts
The last must-know maintenance tip for Kelly bars is
to simply make sure you’re greasing the moving parts. This includes parts like
swivels or bearings that are often in need of lubrication. Keeping them
regularly greased will not only prevent excessive wear, but your equipment will
operate much smoother if the moving parts of your drilling configuration aren’t
constantly grinding against each other and causing friction.