FLORIDA CONTRACTOR BORES MORE THAN THIRTEEN-HUNDRED HOLES THROUGH ROCK WITH NEW ROCK PILOT BIT
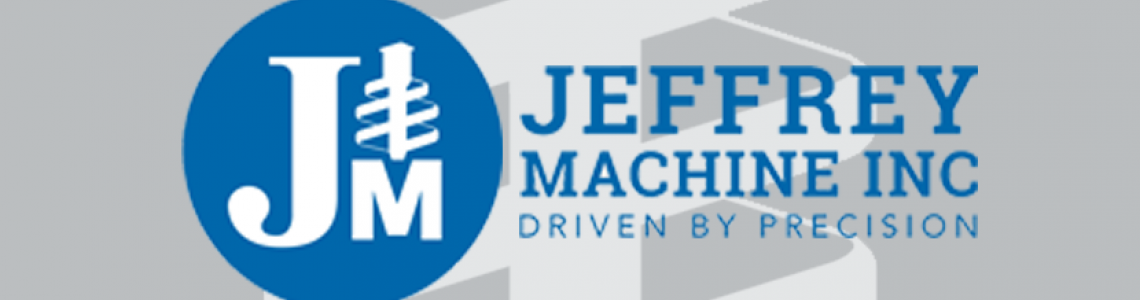
The following article first appeared in the May 2012 issue of The Utility Source and is used here with permission.
The following story tracks how an idea from the field was developed into this incredibly successful rock cutting bit. For those of you who drill holes for utility poles, you know hitting rock can really slow you down. It can chew up bucketfuls of expensive auger teeth and if you have any weaknesses in your equipment, digging through rock will quickly help you find them. Several years back a large electrical contractor got aggravated enough to earnestly search for a solution. Part of the problem was with the round auger teeth that were supposed to rotate in their holders as the auger turned. Rock particles were becoming lodged between the tooth and holder causing it to stop spinning. The combination of pressure and friction against one spot on the tooth would quickly wear it out. If the operator wasn’t careful it could chew through the tooth, the holder and the auger flighting-destroying an expensive auger. There had to be a better way…
They had a number of trenchers and had recently started using a new style tooth in their rock trenchers. The tooth didn’t spin but instead had a huge amount of carbide (a much hardermetal than steel) on the cutting edges of the tooth so it didn’t have to rotate. It cut through rock much faster than the old conical cutters. So if it worked so well on the trenchers, wouldn’t that same thing work in an auger?
They called Jeff Sager whose family owns an auger manufacturing company based out of Birmingham, Alabama. They wanted to know if there was any way he could mount those teeth on an auger. If anyone could do it, Jeff could. Jeffrey Machine has been a southern, family owned business for over three decades. They have amassed a huge amount of knowledge about augers. They enjoy using that information to help contractors solve auger related problems. To paint a better picture of what these folks are like, their attitude reminds this writer of a certain southern gun manufacturer with a current popular reality TV show. They are tight knit, many of them come from the same town, from the same school and they just click together.
New customers are generally surprised when asked questions about the project they’ll be using their tool on, and to learn that the company will custom craft the tool to their application. Even though they have grown into the world’s largest independently owned auger manufacturer, Jeffrey Machine started out as a machine shop. Customizing a tool for the application remains a common practice for them. So, the ones to do it.
Jeffrey Machine took on the project to see if the contractor’s idea of using a stationary tooth would work. They hard welded the trencher teeth to the auger just to give it a try. It ended up working beyond expectations. Unfortunately the teeth eventually wear out, even though they far outlasted the standard round ones. With the bits hard welded the contractor had to send the auger back to the factory to change out the teeth. A whole new tooth and holder system would have to be developed so the cutting bits could be easily replaced. The process took several years and even included a trip to an area of Germany famous for the highest grade carbide.
Humorous side note: Jeff was forced to learn some basic German for his travels. One of his English speaking German counterparts laughed when he heard him. He said it was the first time he’d ever heard anyone speak German with an Alabama accent.
Most generally projects don’t lead to globetrotting, but Mr. Sager considered this important enough to go as far as it took to make it happen. The end result is a stationary rock drilling bit and holder system designed specifically for use with derrick augers. The “Dragon’s Tooth™” system works incredibly well on a large variety of rock conditions and more than satisfied the contractor’s needs.
How effective has it been? One contractor recently ran into some tough rock in Rainesville, Alabama. With standard teeth it took thirty minutes to penetrate six inches. Switching to the bolt on Dragon Tooth system, using the same machinery on the same rock they penetrated twenty four inches in thirty minutes. That’s equates to a four hundred percent increase in productivity with a whole lot less wear and tear on the machine. Oh, also the round teeth were ruined whereas the Dragon Teeth were undamaged. Not bad. Of course, just to be realistic, you may or may not experience the same results or your results might be much better. There’s a whole lot of different types of rock and they all vary when it comes to drilling. There is not a one-size-fits-all solution, but this is definitely one tool system you may want to seriously consider adding to your tool kit.
Let’s have a look at the guy that drilled over thirteen hundred holes with a Dragon Pilot Bit. Sam Stoia owns and operates AAA Quality Docks & Boatlifts Of The Keys in Key Largo, Florida. Mr. Stoia keeps a crew pretty busy digging holes along the shore with a derrick drill rig set up on a barge. He uses a standard 18” derrick auger with standard bullet teeth. He has added some punch to it with a Dragon Pilot Bit. The pilot holds four Dragon teeth and a round carbide center point. When questioned about how hard the coral rock is compared to other rock, Sam comments, “There is no soft stuff (Key Largo, FL) to speak of and that’s what your dragon toothed tip has performed wonderfully on. It’s still sharp, it’s still good.” Commenting about the digging conditions through their coral formation, “the friction is immense and we go through the stainless wear bars pretty fast on the outside edges of these things. We go through the bullet teeth too but we haven’t gone through the dragon teeth yet.” At the time of the interview they had punched over a thousand holes with little to no obvious wear on the teeth. I just received word that he’s now drilled over thirteen hundred holes. Sam added, “That Dragon Tooth pilot just keeps working like a son-of-a-*#@!! (sailor talk).” He likes it. So if you have a job around the Keys and need some offshore drilling, Mr. Stoia is the man to contact. www.floridakeysmarineconstruction.com.
So in summary when companies listen and care enough to go the extra mile, it can become a wonderful source for useful new product ideas. An old-timer in the utility construction industry once told me, “Lis-ten to the guys in the trenches. If you’ll just shut up and listen, they’ll tell you what they need.” His advice has proven to be correct in this case. A successful product devel-oped from the field for the field will typi-cally find a plethora of new applications, just like the Dragon Tooth finding a perfect use cutting holes in sea beds. Kudos to Mr. Sager and his team for listening and coming up with a better rock cutting solution for augers in the Dragon Tooth invention.
COMPANY PROFILE: BIG SHOP WITH SMALL SHOP SERVICE!
Jeffrey Machine Incorporated (www.jeffreymachine.com) has become one of the largest auger manufacturers in the world but they offer the highly personalized service you might expect from a small machine shop. Starting out as a machine shop in 1977 they began designing augers for local contractors. The company experienced an explosion of growth as word spread about the quality tools they were producing. They went from a modest nineteen thousand square foot office and shop to their current 100,000’ state of the art facility. Unlike big corporations that have been repeatedly bought, sold and merged, Jeffrey Machine is privately owned. So essentially all the experience they have acquired hasn’t been lost in a corporate cloud but is available to help with your particular drilling tool needs. Located in Birmingham, Alabama their facility includes a mammoth flighting press with capabilities to press everything up to twelve feet diameter by two inch thick flighting. They have a huge computerized laser/plasma cutting table that will quickly carve up enormous slabs of steel into any type of flighting imaginable. Top notch machinists, welders and every piece of equipment needed to customize anything on the fly has been provided. That of course includes robotic welders, CNC’s, and soon to be added will be a rolling press to roll up to 2” thick plates of steel into barrel formations. These are used for core barrels, clean out buckets, etc. Jeffrey Machine’s skills have branched into all types and kinds of derrick augers, foundation augers, utility vehicle accessories and untold thousands of one of a kind tools crafted for an individual contractor’s needs. Visitors are wowed by how big everything is, how friendly the people are, how clean it’s kept and how efficiently everything is set up.