Jeffrey Machine Corporate Profile for Piling Canada
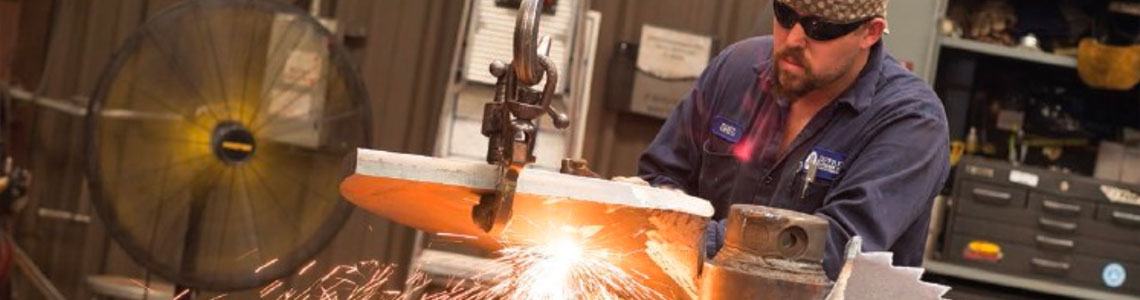
HISTORY
In 1977, Frank Sager opened the doors to Jeffrey Machine (named for his son and current owner Jeffrey Sager) as a small machine, tool and die shop in Birmingham, Alabama. Frank Sager, a machinist and metal fabricator with many years of experience, created tools to the exact design request of his customers. Jeffrey Sager joined the family business in 1986. He learned his Dad’s trade of being a Machinist first but began working primarily with augers shortly after that, first repairing them and later rebuilding them often resulting in a better tool than the original one. It was a natural progression to fill the auger market demand and to begin manufacturing better tools to hold up to Alabama’s limestone and rocky soil.
“Our very first auger customer was Alabama Power, we had instructions from them for utility needs and we got to work. We delivered and they are still a valued customer today,” says Jeffrey Sager adding “This is when we started to break into the utility category and moving into other markets in and around Alabama.”
GROWTH
In 2001, a 20,000 square foot shop was built, and due to increasing demands, another of equal size was constructed in 2002. Another expansion completed in 2007 brought the facility to over 100,000 square feet, making Jeffrey Machine one of the world's largest independent auger manufacturers. “When we purchased this property, we knew we would build our facility to meet our needs and that it would allow us to continue to grow. We have an additional 14 acres if we need it" says Sager.
The period of 2002 to 2014 was one of heavy growth and included the addition of three Outside Sales Reps to manage the territories across the US and adding fifty production workers and office staff. In addition to growth in the US, we grew to the Canadian Market and began offering foundation and utility with dealers. We currently work with Pinnacle Drilling and ML Air for foundation tooling and Commercial Truck for utility tooling. Sager adds “Canada is a very promising market and we have a great deal of success with the dealers we have chosen to work with there. Canada can have some very challenging conditions to drill in but we have listened to what our customers needs are and modified tooling to meet those challenges.”
In 2016, celebrating their 40th anniversary, Jeffrey Machine, introduced a unique, new feature – crimson red coating on all tooling. With this bright new finish on our products, they not only stand out for their unmatched quality and it also makes them instantly recognizable as tooling produced exclusively by Jeffrey Machine.
In 2017, they added a Euless, Texas branch. This facility focuses on selling consumables such as pilots, adapters, teeth, holders and shaft spacers; and carries items such as Slurry Products, Polybore, Quick Gel and EZ Mud Plus so that customers can access them quickly and directly. They also offer a full line of stock tools. “Contractors having quick access to tools is an especially important aspect of this industry. Decreasing down time is a way we can lead in customer service. Adding the Texas location so that we can ship faster to different areas of country was a game changer for us,” says Sager.
In 2019, Sager’s children both joined the family business. Sam Sager, as Director of Operations and Gabby Sager, as Marketing Manager. “It is a great feeling to now have the third generation in place at Jeffrey Machine. I know my parents would be very proud. I looked forward to this day for a long time and I have enjoyed watching them immerse themselves in day to day operations and make our Jeffrey Machine family even stronger. Our greatest asset at Jeffrey Machine is our employees and we want them to always feel valued and important - that is the main principal I want them to carry on,” said Sager.
TOOLING|FACTORY
Their state-of-the-art facility uses both standard and proprietary equipment, including a game-changing Plate Roll. The Plate Roll greatly increases their capacity to quickly roll cylinders of up to two-inch thick material up to 10 feet long, and in diameters as small as two feet and as large as 15 feet, making it perfect for barrels, cylinders and coring products that need a quick turnaround from shop floor to job site. This custom Plate Roll was a huge investment that has paid off by greatly improving the factory’s ability to be more responsive to customers’ needs and adding new areas of potential expansion into new markets.
We have a partnership with BETEK GmbH & Co. KG, one of the foremost global manufacturers of wear parts incorporating tungsten carbide. Our revolutionary .990 dirt tooth is designed by Jeffrey Machine and manufactured in partnership with BETEK. This unique tooth is engineered for use with a multi-purpose type auger equipped with a .990 TRI Holder. The versatile TRI Holder is uniquely designed to accommodate three different types of teeth: the new .990 dirt tooth; the standard .990 tooth (known in the industry as C-31); and Jeffrey Machine’s exclusive .990 Dragon’s tooth.
Proprietary to Jeffrey Machine, the .990 tooth is unique in that the shank of the tooth will fit in a C-30 holder (or pocket), which is machined in-house from 4140 high tensile steel. The benefit of this interchangeability is that is allows contractors to move easily from a project in a rocky environment that requires a conical rock tooth or Dragon’s tooth, for example, to one in a non-rocky condition using the .990 dirt tooth in the same tool. This interchangeability helps significantly reduce project set-up time, as well as costs that result from the need to transport multiple augers to project locations.
Development of each innovative Jeffrey Machine product is the result of extensive field study and an enduring commitment to constantly improve the safety and performance of every product. Working side-by-side with their customers, Jeffrey Machine creates drilling tools with enhanced capabilities as unique as the demands of each job. Jeffrey Machine offers a comprehensive line of auger tooling manufactured to ensure optimal performance under the most demanding drilling conditions. At the heart of this leading manufacturer of some of the world’s toughest tooling is a precision machine shop that is small enough to continue providing exceptional, personal service. “My father expected excellence every day from employees and in every piece of tooling that left the factory. He set the bar high for us and I expect the same results from the employees and tools we manufacture today. With that in place, I feel like the future is bright,” said Sager.