NORTH CAROLINA CONTRACTOR HITS IMPREGNABLE ROCK
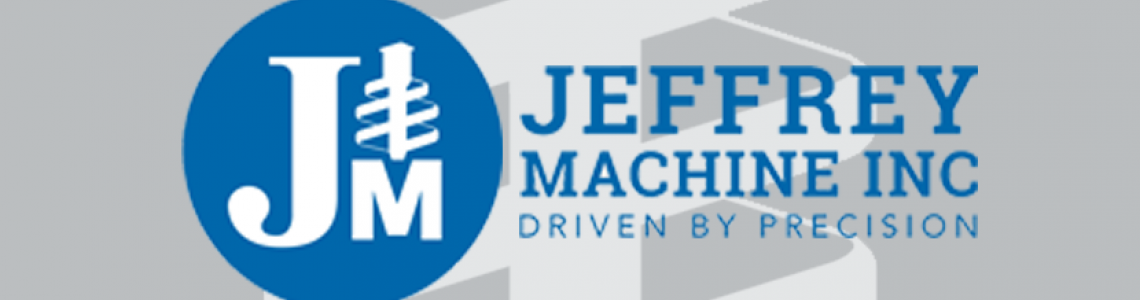
This article written by Bob Green first appeared in the Jan/Feb 2013 edition of the IMSA Journal and is used here by permission.
Drilling a five foot deep hole in rock shouldn’t be a problem with a pressure digger and a good rock auger. Haynes Electric Utility Corp., one of eight divisions of MB Haynes Corporation is based out of Asheville, North Carolina and holds several main-tenance contracts with the North Carolina Depart-ment of Transportation (NCDOT). Rock boring for utility pole installation is a common necessity in that part of the country and Haynes has done scores of them. On this project, a flashing signal light needed to be installed on a two lane road near the top of a mountain.
THE NEED
Traffic at the intersection of Dillard Rd. and Old Mud Creek Rd. has been steadily increasing for the past several years. Dillard is the main highway and Mud Creek dead ends into it. The increase in traffic going to and coming from Mud Creek is due in large part to a multi-million dollar upgrade to the Sky Valley Golf Course which is accessed via the Mud Creek intersection. The summertime population of the resort area is about thirty five hundred residents and visitors.
According to Milt Gillespie, one of the resort owners, they have one of the “most beautiful golf courses in the southeast. Our elevation is 3300 to 3500 feet. The ball flies a little bit further up here and it’s always a little bit cooler.” If you decide to go play the course, word of caution, bring plenty of balls. The record has been thirty-six balls lost on the first nine! Any-way, back to the story; the intersection has always been bad, but the heavier flow of traffic has made it that much more dangerous, resulting in more bad accidents. A rock bank to the left, steep hill and close curves in both directions provided a limited view of oncoming traffic from either direction.
According to one of the area residents, you had to look both ways, pray and punch it hard to make it off Mud Creek and onto Dillard with your life and vehicle intact! To alleviate the problem the D.O.T. sent in a track hoe earlier this year with a rock hammer to take out a chunk of the bank at one corner providing more visibility. The other thing they did was to send in M.B. Haynes crew to set up an actuated flasher at the juncture. As part of that installation, several poles would need to be set. Four poles would be set at the intersection and another one about 200 yards down the mountain for an approach flasher. Five – 18” diameter holes drilled five feet deep would need to be drilled for the poles, so a crew was dispatched and started the first hole.
THE PROBLEM
After an entire day of grinding away, the drilling crew had penetrated less than a foot. The Peterbilt truck with the pressure auger was providing plenty of pressure, torque and power, but the result that first day was a number of broken and worn out bul-let style teeth the rock auger used. The same thing. happened for the following three days. They had run into something known locally as “Blue Granite” (the crew had other more descriptive words for it).
Haynes’ drill rig operator, Eddie White, had this to say, “The rock was blue granite but we had never run into anything as solid as that was. That was some of the hardest drilling I’ve had to do.” He continued, “We went through quite a few of the bullet teeth. They seemed to break off more in the rock than wear out. It would hang on a crack in the rock and break. That happened pretty often.” A project observer commented on one of the days they were drilling, “they hit a little bit of water and when they pulled their auger out it had burnt up all their bits on the bottom. It was so hot that the water (in the hole) was boiling.”
Burning up and breaking off the bits is one thing, but a good operator can typically sense when the teeth are going bad and will pull the tool before it goes too far and destroys the auger. Mr. White has been doing this type of work for years. When asked how he can tell, he said it’s pretty easy when there is water in the hole. He explained that when the teeth are intact you will see fragments of rock and water coming up on the auger screw (flighting) as it’s turning. When the teeth cease to cut it turns more to the consistency of mud. He said you also take into consideration a number of other factors that might spell trouble such as the way the machinery feels or even from the odors coming up from the bore hole. According to Nathan Taylor, Hayne’s Traffic Signal division’s project manager, they decided to postpone the project until they could come up with something more effective for boring that rock.
THE SOLUTION
Nathan had heard about a different type of rock cut-ting bit made by the same company that made their augers. Initially made for derrick augers, they had recently developed a larger .990 sized tooth to accommodate pressure augers. He’d heard good things about it but never tried it. This project needed something more than what they had and this would be the perfect test to see if it lived up to its rock cutting reputa-tion. Mr. Taylor contacted Tony Crocker with Jeffrey Machine (www.jef-freymachine.com) and ordered an 18” pressure auger fitted with the special bits. Unlike the round bullet tooth that holds a tip of ultra hard carbide and rotates in the holder as the auger turns, the Dragon’s Tooth doesn’t rotate. Instead it’s held in a stationary position. It uses twice the amount of carbide found in a bullet tooth but deploys the carbide along the angular cutting edge where it purportedly cuts more aggressively into the rock.
THE RESULT
Eddie White wasn’t impressed. In his words, “When I first saw it, I didn’t know if it was going to work or not. To me it didn’t look like it was going to be able to do what I needed it to do. The teeth looked too big and I was thinking I needed something with more of a point on it to where it would cut.” He and his crew were sent with the new auger back to the Mud Creek Rd. location. They dropped the new drill into the half bored hole and immediately started making progress. Starting where they had left off several weeks earlier, they were able to finish that hole and drill two more through the same rock before the day was done. The following day they finished the last two holes. This auger set up with the new teeth provided an astounding twenty-five hundred percent increase in hole-cutting production over the standard bullet teeth. Additionally, none of the Dragon Teeth had to be replaced – all the damage was done to the rock instead. Reflecting on his ear-lier comments about not thinking the auger would work he com-mented, “I was fooled. It worked. Whoever designed that – it was a good design.”
Delving a little further into the story of how this new cutting system was developed, in a con-versation with the auger company it was learned that the idea for it had actually come from one of their customers. That contractor had recently started using non rotating teeth in trenchers and mining equipment. They worked so much better than the rotating bit she requested Jeffrey Machine hard weld some of those teeth into an auger just to test it out. It worked wonderfully, but when the teeth eventually wore out, replacing them was a real hassle.
The challenge was to come up with a holder that would hold the tooth stationary yet allow for easy replacement. Additionally, it would be great to develop a holder system that would accept standard round bullet teeth as an additional option. The process took several years but what they have developed has provided a viable solution to otherwise seemingly impossible situations like M.B. Haynes faced in Haywood County, North Carolina.
“These pressure diggers are essential to our work in this rocky, mountainous terrain. Our long-term relationship with Jeffrey Machine and their products enables us to deliver efficient, high-quality work to our customers,” said Nathan Taylor. The most important thing in this case is that both residents and visitors in Sky Valley are grateful for the additional safety provided by the warning light and refurbished intersection.